Case Studies
As of early 2023, Liveline Technologies has deployed our advanced factory automation on more than 20 production lines spread across 7 facilities and 4 countries. Most of our applications have focused on various types of extrusion processes, as desired by our lead customers. However, our technology is well suited for almost any continuous manufacturing process, such as fiber optic cables, thin films, and food & beverage production — see the discussion here.
Here are some of our success stories:
Reactive extrusion
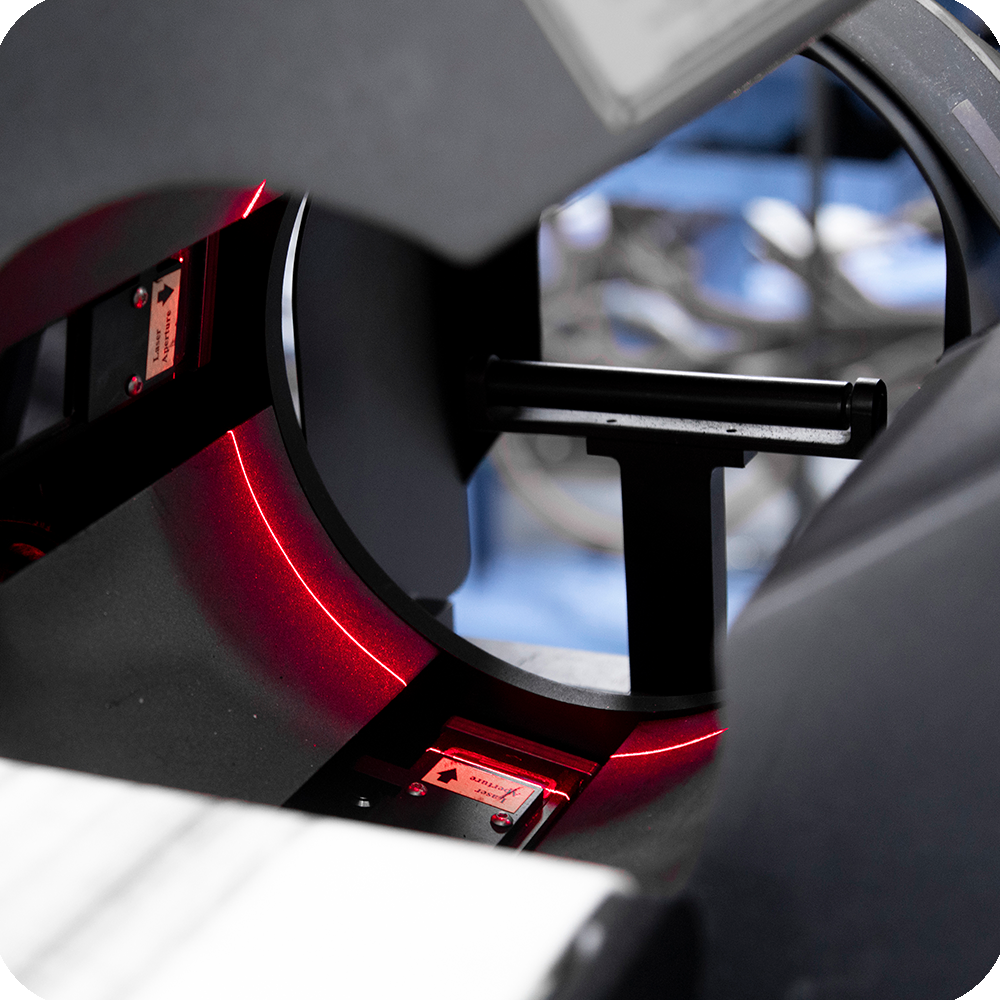
The production lines each utilized four large extruders with flows that combined into a single continuous profile. Each extruder produced a different polymeric material, and all of them utilized reactive extrusion (polymerization initiated by injecting chemicals into the extruders). The customer suffered from unstable output due to natural variations in raw materials and plant conditions.
We deployed on three production lines in this facility and achieved:
39% reduction in scrap and waste
82% reduction in unplanned line stops
Payback < 3 months
Thermoset extrusion

The production lines utilized multiple large extruders feeding a complex die that combined the material flows around a metallic backbone. Extruders utilized various synthetic rubber compounds, and polymerization was performed by a series of gas-fired ovens downstream. The customer wanted to improve dimensional stability of the final parts and reduce the hourly interactions required by a line operator.
We deployed on two production lines in this facility and achieved:
47% reduction in dimensional variation
21% to 55% reduction in line scrap
Runs exceeding 12 hours with no operator interventions
Payback < 6 months
Thermoplastic extrusion
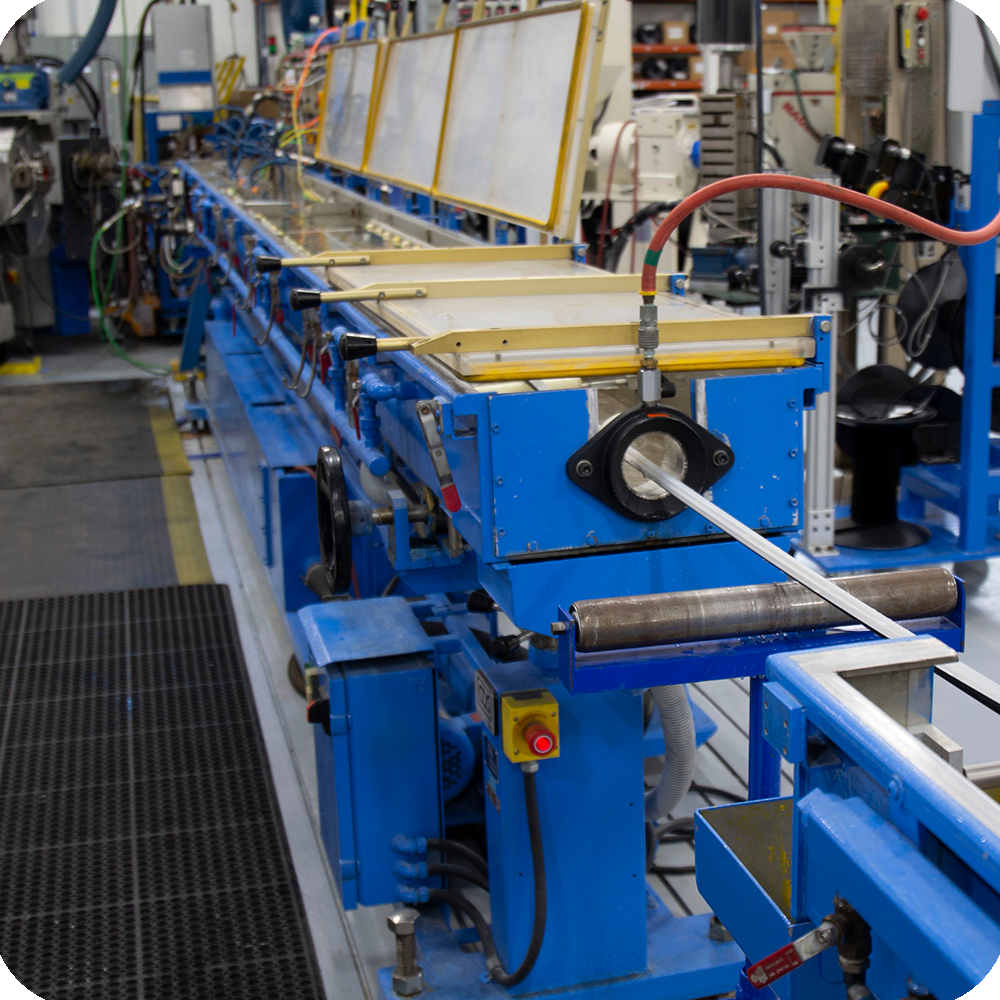
The production lines utilized multiple large extruders that combined material flows into a complex profile produced at high speed. Materials were thermoplastic polymers, and the profile geometry was stabilized by a cold-water bath downstream of the extruders. The customer wanted to improve dimensional stability of the final parts and reduce the hourly interactions required by a line operator.
We deployed on two production lines in this facility and achieved:
54% reduction in dimensional variation
Runs exceeding 12 hours with no operator interventions
Payback < 6 months
Other benefits
Our advanced factory automation delivers tangible improvements in cost, quality, and environmental footprint (click here to learn how).
Because our automation is based on predictive AI controllers, we know how the production lines will evolve in the near future, and can provide predictive alarms. This allows for significant cost avoidance.